Customer Stories
For over 25 years, OptimEyes/HLImage++ has been used to solve a vast array of customer problems. Some of the projects undertaken by our predecessor, Western Vision Software, are described below.
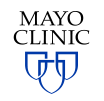
In order to analyze tissue samples, the clinic was using a Proteome Profiler™ Antibody Array kit from R&D Systems (www.rndsystems.com), which needed to be analyzed. We gathered the requirements from the clinic, and then contacted R&D support to make sure we understood it correctly. Next, we used the individual HLImage++ tools to process the images from the kits, but it was a multi-step process that the clinic found confusing. Thus, we took the individual steps, and easily created a custom tool that was specific to doing the needed ‘Array Analysis.’

(Ideal Eyes Systems has continued development of QuickSpots, expanding the list of array models that it supports to include many from Abcam and RayBiotech, and making it quicker and easier to use than ever.)

When a goniometer company needed to write an entire contact measurement software application, including camera support, they contacted Western for a quote.
They found our pricing much lower than the next lowest bid, and then found out the reason:
With HLImage++, we were starting with an application that was already 100% completed, documented, and well tested.
While the others needed to start from scratch, we simply had to write a few new tools, and we were done.
The result was a renamed version of HLImage++ and a specific set of tools for doing contact measurements.
This application was created in 1998, was very successful, and is still in use by scientists today.
The product contained HLImage++ and six custom tools:

- Contact Angle Tool: which characterizes the behavior of a liquid on a solid
- Pendant Drop Tool: which determines the profile of a pendant drop or bubble at hydrostatic and interfacial equilibrium and consequently determines its surface energy value
- Acid-Base Tool: which evaluates the surface energy parameters of a given solid using the contact angles of three different test liquids
- Surface Energy Tool: which evaluates the surface energy of a given solid using the contact angles of different test liquids
- Work of Adhesion Tool: which determines an index of wetting ability of a liquid for a solid
- Zisman’s Plot Tool: which summarizes wetting behavior and allows predictions of an interpolative nature using a homologous series of liquids
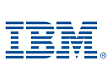
When process engineers at IBM San Jose were searching for methods to increase productivity and improve quality control,
they contacted Jim Saudargas of Concepts in Computing, a company from Beloit, Wisconsin, to provide them with a solution to inspect wafer slices composed of disk drive heads.
As Saudargas started to design the inspection machine he recalls, “I knew the key aspect of this application was going to be the software. I needed software that was powerful, yet flexible, so I could customize it to fit my needs.” The software solution chosen was Western Vision Software’s machine vision package HLImage++.
Using HLImage++ Saudargas was able to design and write a custom application with a fully functional user interface. The requirements set forth by IBM called for a three-dimensional inspection of the drive heads that incorporated 83 different measurements. The measurements taken had to be accurate and repeatable to one-half micron (40 millionths of an inch). Requirements included X, Y, and Z (height) measurements. Also, each of the 10 to 24 rows of heads to be inspected had to be checked for alignment and parallelism.
After completing the project successfully, Saudargas stated: “HLImage++ really works. Its flexibility is unsurpassed in the industry.”
Saudargas has continued to work with Western Vision over the years and has created many successful inspections machines using HLImage++.
As Saudargas started to design the inspection machine he recalls, “I knew the key aspect of this application was going to be the software. I needed software that was powerful, yet flexible, so I could customize it to fit my needs.” The software solution chosen was Western Vision Software’s machine vision package HLImage++.
Using HLImage++ Saudargas was able to design and write a custom application with a fully functional user interface. The requirements set forth by IBM called for a three-dimensional inspection of the drive heads that incorporated 83 different measurements. The measurements taken had to be accurate and repeatable to one-half micron (40 millionths of an inch). Requirements included X, Y, and Z (height) measurements. Also, each of the 10 to 24 rows of heads to be inspected had to be checked for alignment and parallelism.
After completing the project successfully, Saudargas stated: “HLImage++ really works. Its flexibility is unsurpassed in the industry.”
Saudargas has continued to work with Western Vision over the years and has created many successful inspections machines using HLImage++.
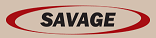
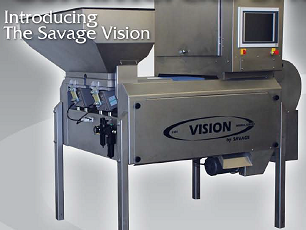
The task was to make a software product that would grab high speed images of good and bad nuts as they flew by the camera, separate touching objects, inspect and analyze them, and then eject everything but good product; and to do it all in under 10ms.
To accomplish this task, we used HLImage++ and its set of imaging tools to determine the best method. The process was recorded in a Point & Click Script, and well tested. The script was then exported to an embedded script and run with HLEmbedded and Windows Embedded. To control the critical timing, a custom mini-tool was written with an embedded queue, to control the needed Digital IO.
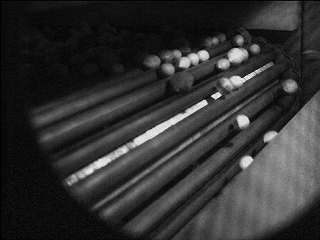
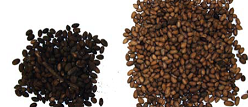
(Refresh browser to restart slow motion video of nuts being ejected.)

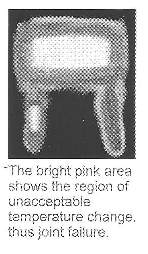
The project was successful, and having eliminated the need to hire an outside company to test and inspect the welds, the coil manufacturer now inspects 100,000 parts per day. See the entire story as printed in Photonics.

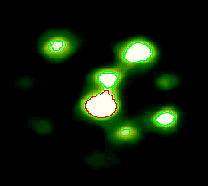
In order to relate the structural characteristics of the atom clusters to the electronic properties of the clusters they would need accurate measurements and statistics. HLImage++ was the software chosen to deliver this data. HLImage++ is an object-oriented machine vision and image processing package that has excellent out of the box tools and according to Dr. Lovall is “much better than anything we had used before”
(Cover story of Advanced Imaging Magazine...)
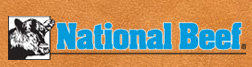
Did you know that the beef, chicken, and other meat you purchase in the store must have a thin layer of air between the film dome of the covering plastic and the meat?
Turns out, if that small pocket of air is not present, then the meat will touch the plastic.
When this happens, the meat can go bad.
Similarly, when the meat is packaged, small parts can fall in the seal between the tray and the plastic wrapping, which can also lead to bad meat.
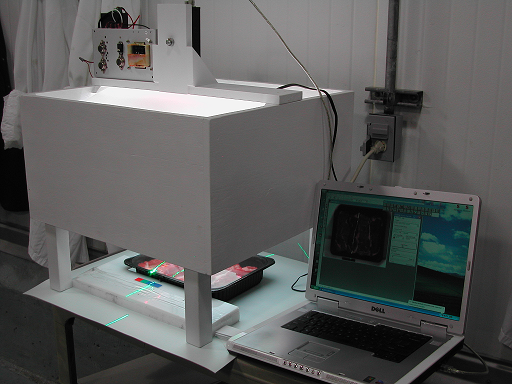
This is the test setup that was used to determine how to solve the issue using a fan laser at a given angle to the product.
Western worked with National Beef to make a product inspection system that makes sure there is no meat in the seal and the meat is not touching the film dome of the packing.
After determining the lighting, laser, and laser fan angle, we started off by gathering thousands of images of meat in trays as they came down the line at the National Beef plant in SLC Utah.
Next, we used the large set of HLImage++ tools to write (2) separate Point & Click scripts, which we appropriately called:
When we had both of the scripts fully working, we combined them, exported them to a single embedded script,
and provided an excellent solution running on Windows Embedded, which was later patented.
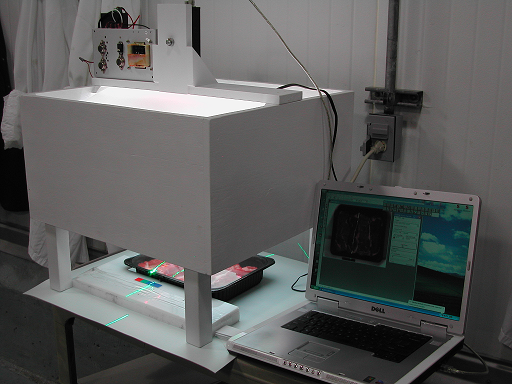
This is the test setup that was used to determine how to solve the issue using a fan laser at a given angle to the product.
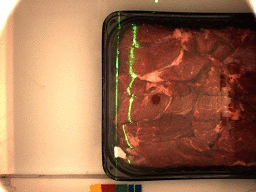
|
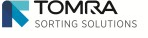
Ever wonder why the fries, potato skins, and other potato products seem so different from one restaurant to the next?
Part of that difference is due to the amount of peel left on the potato at the processing plant that makes the product.
In the sweet-smelling town of Quincy Washington (the small town actually smells like potatoes),
we learned all about it as we helped Tomra-Odenburg develop their next generation of Peel Quality Monitoring & Control products.
The task was a large one.
First, we had to determine the proper lighting, camera, belt speed, etc, to get excellent images without glare of wet shiny potatoes.
Next, we had to separate all touching potatoes as they came down a conveyer, so we could measure each one for:
Next, we needed to deliver all of this information over the network, to allow a PLC to do analysis and control the desired peel amount.
Next, we had to create a full-blown method of allowing the plant operators to tweak the color for each classification (Flesh, Peel, Rot, Bruise, and Green) as the potatoes changed colors during the season and in storage.
Last, it was demanded that the entire solution run 24/7 without a single restart for 2 months, or the entire system would be returned.
The solution was a 3-color camera, optics, and filtering, to provide the glare-free images with excellent color.
After collecting thousands of images in the plant, the HLImage++ tools were used to create a solution in the form of a Point & Click Script.
Once the script was finalized and well tested, it was exported to HLEmbedded.
Windows Embedded was used so the solution would run 24/7 without a single restart.
In order to easily allow the line operators to classify the colors (in 3D RGB space),
a separate application was written to interface with the script running in HLEmbedded.
This allowed proper peeling of the potatoes as they changed colors from day to day in storage.
The system was delivered to Quincy, where it ran 24/7 for months and months without a single restart, and provided a huge cost saving by providing accurate peeling. The plant purchased a second unit, and Tomra-Odenberg has been selling the system worldwide for over 10+ years.
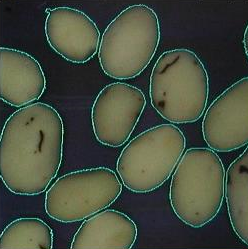
|
Next, we had to create a full-blown method of allowing the plant operators to tweak the color for each classification (Flesh, Peel, Rot, Bruise, and Green) as the potatoes changed colors during the season and in storage.
Last, it was demanded that the entire solution run 24/7 without a single restart for 2 months, or the entire system would be returned.
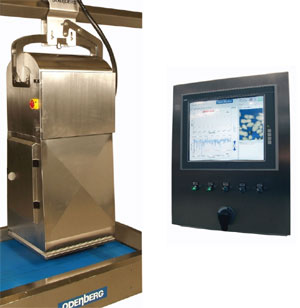
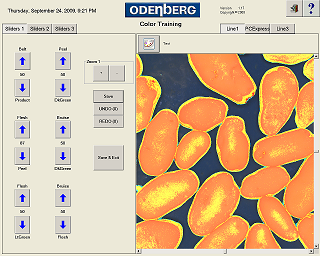
The system was delivered to Quincy, where it ran 24/7 for months and months without a single restart, and provided a huge cost saving by providing accurate peeling. The plant purchased a second unit, and Tomra-Odenberg has been selling the system worldwide for over 10+ years.

When a large manufacturer of packaging equipment wanted their own version of machine vision software, tailored to their needs, they came to Western for a solution.
Western worked with them to produce a product they could call their own.
The goal was to make a software vision inspection system, which could identify any product that could be run on any given line, inspect it, and then tell a down-line labeler what the product was, so it could automatically be weighed and labeled correctly.
The task was difficult, as most cuts of meat share very similar traits. They are all reddish, meat, and come from the same animal. To solve this task, we took hundreds of images and used the built in HLImage++ tools to measure different criteria. We then created the answer tool, which is a classification tool (similar to a neural network, but easier to understand). The measured criterion was then fed into the Answer tool to classify the product. It was decided that if no clear classification could be automatically determined, then a pop-up would let a user select the correct product.
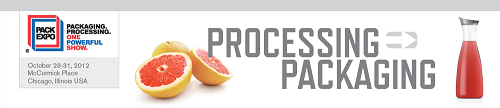
At the next pack expo, they unveiled the first version of Bizerba Vision…
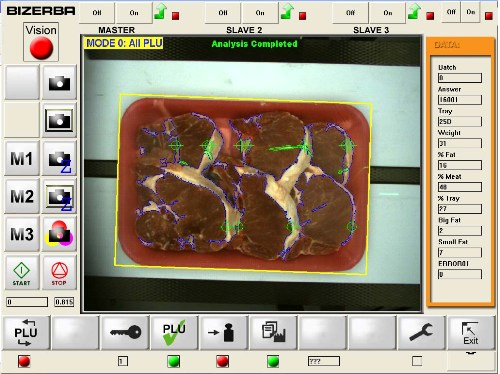
The result was a HLImage++ script, a set of custom mini tools, all exported to a HLEmbedded script running under Windows Embedded, as shown here.
The goal was to make a software vision inspection system, which could identify any product that could be run on any given line, inspect it, and then tell a down-line labeler what the product was, so it could automatically be weighed and labeled correctly.
The task was difficult, as most cuts of meat share very similar traits. They are all reddish, meat, and come from the same animal. To solve this task, we took hundreds of images and used the built in HLImage++ tools to measure different criteria. We then created the answer tool, which is a classification tool (similar to a neural network, but easier to understand). The measured criterion was then fed into the Answer tool to classify the product. It was decided that if no clear classification could be automatically determined, then a pop-up would let a user select the correct product.
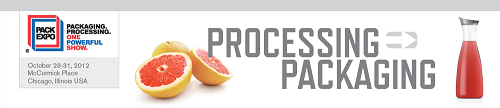
At the next pack expo, they unveiled the first version of Bizerba Vision…
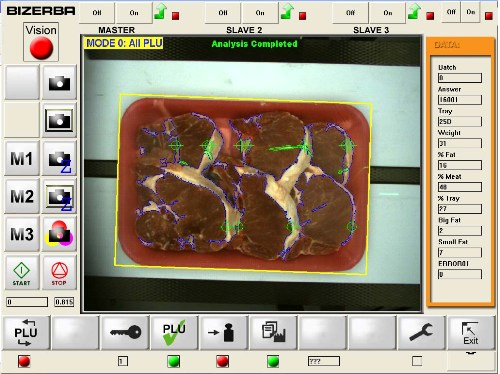
The result was a HLImage++ script, a set of custom mini tools, all exported to a HLEmbedded script running under Windows Embedded, as shown here.
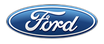
When Ford wanted to inspect its radiators for damage, they contacted a California system integrator, who used HLImage++ to do the job.
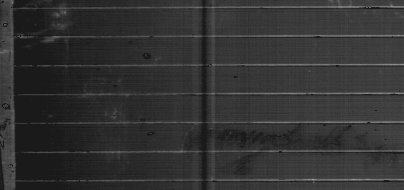
With the correct lighting, a stepper motor control system, and the HLImage++ line profile tool, the job was a rather easy one. By simply moving the camera a known distance, and running multiple line profiles across each image, the task was easily accomplished.
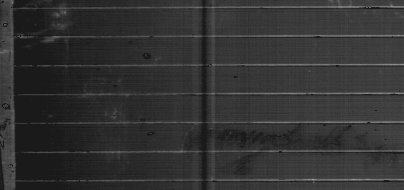
With the correct lighting, a stepper motor control system, and the HLImage++ line profile tool, the job was a rather easy one. By simply moving the camera a known distance, and running multiple line profiles across each image, the task was easily accomplished.
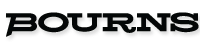
When a large electronic manufacturer wanted to check their resistors and other components for lead straightness, they contacted Western for help.
During a visit to their plant, in under a few hours we showed them an easy solution.
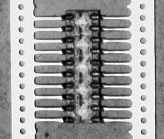
We simply took a picture with a camera and some simple lighting, and then took multiple line profiles by setting up a Point & Click Script to move a line profile across the leads of the components.
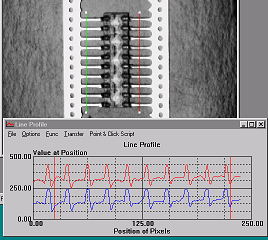
By using several line profiles, we could determine if the leads were straight or damaged.
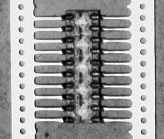
We simply took a picture with a camera and some simple lighting, and then took multiple line profiles by setting up a Point & Click Script to move a line profile across the leads of the components.
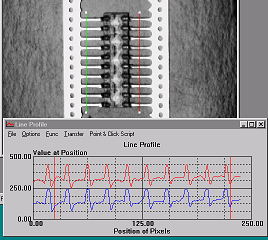
By using several line profiles, we could determine if the leads were straight or damaged.
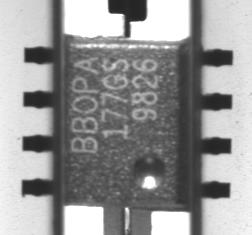
When a small system integrator needed to check the placement and leads of ICs for damage, they turned to Western for expertise and support.
The task was easily accomplished using the Line Profile Tool in a simple Point & Click Script.
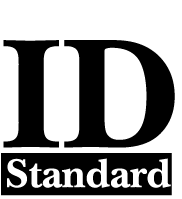
The Mexican government was having issues with driver license photos.
The images of the people were not being taken correctly, and the result was not being able to sometimes tell who the person was on the ID.
They contacted the ID Standard company of California, who came to Western for a solution.
The task was to design a camera that would automatically find a person’s head, center it, zoom to the correct amount to correctly fill the screen, and then take the image. Cost was also important.
Using HLImage++, we designed up the software to do the task at hand. In addition, we used Solidworks to make a moving holder for a camera, so it could capture the tall and the small. We then designed up a USB stepper motor controller from the chip level to keep cost down. Last, we wrapped it all up in an easy-to-use custom application using the HLImage++ API.
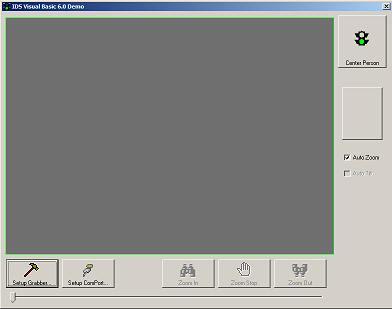
The result was a fully automated system, with manual override control. It provided a low-cost full-blown solution which was easy to use.
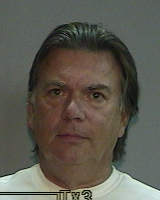
The owner of the ID Standard Corporation loved the solution, as you can see here with his photo ID automatically perfectly zoomed and centered, using the solution.
They contacted the ID Standard company of California, who came to Western for a solution.
The task was to design a camera that would automatically find a person’s head, center it, zoom to the correct amount to correctly fill the screen, and then take the image. Cost was also important.
Using HLImage++, we designed up the software to do the task at hand. In addition, we used Solidworks to make a moving holder for a camera, so it could capture the tall and the small. We then designed up a USB stepper motor controller from the chip level to keep cost down. Last, we wrapped it all up in an easy-to-use custom application using the HLImage++ API.
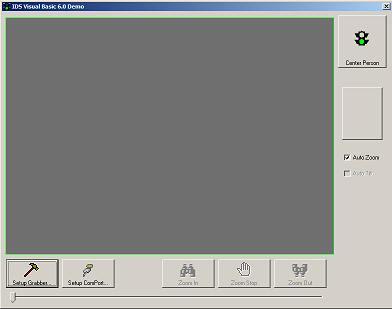
The result was a fully automated system, with manual override control. It provided a low-cost full-blown solution which was easy to use.
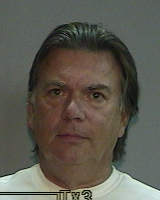
The owner of the ID Standard Corporation loved the solution, as you can see here with his photo ID automatically perfectly zoomed and centered, using the solution.
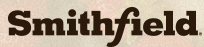
When Smithfield Hams wanted to modernize one of their plants, they called in a system integrator to redo the entire plant.
Part of that upgrade was to build a vision system that would classify what type of ham part was coming down the line, inspect it, grade it, and then communicate that to a labeler.
In addition, all the statistics from each product was placed into a database.
The solution was a two-camera system.
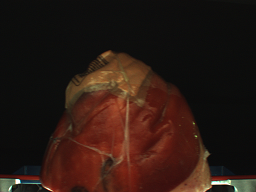
A side camera was used to determine the part type.

A bottom camera was used to inspect the face of the product.
Because the color inspection was critical, known colors were placed in the field of view that could be used as a base line. Depending on the part type, one of several inspections would be used to determine the grade of the product:
After determining how to grade, thousands of images were collected, and each test was developed independently as a separate Point & Click Script.
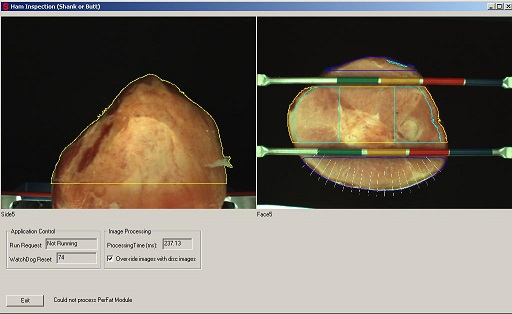
When each independent script ran to satisfaction, they were combined into a single custom application using the HLImage++ API.
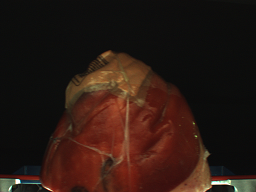
A side camera was used to determine the part type.

A bottom camera was used to inspect the face of the product.
Because the color inspection was critical, known colors were placed in the field of view that could be used as a base line. Depending on the part type, one of several inspections would be used to determine the grade of the product:
|
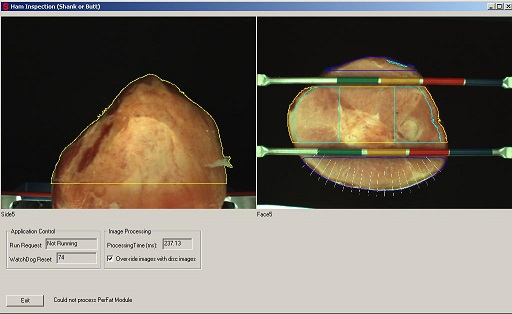
When each independent script ran to satisfaction, they were combined into a single custom application using the HLImage++ API.
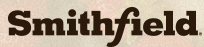
When Smithfield Hams wanted to modernize one of their plants, they called in a system integrator to redo the entire plant.
Part of that upgrade was to build a vision system that would check ham slice packaging for leaks in the packaging.

The perimeter of the ham was followed and inspected at each point with a custom inspection routine. The routine was determined by using the HLImage++ Tools in a Point & Click script.
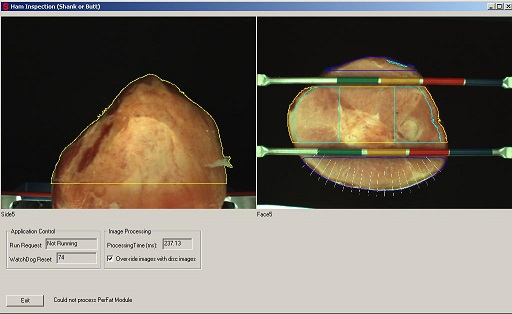
When completed, the script was run to do the inspection. When a bad leaker was detected, it was ejected from the line using Digital IO.

The perimeter of the ham was followed and inspected at each point with a custom inspection routine. The routine was determined by using the HLImage++ Tools in a Point & Click script.
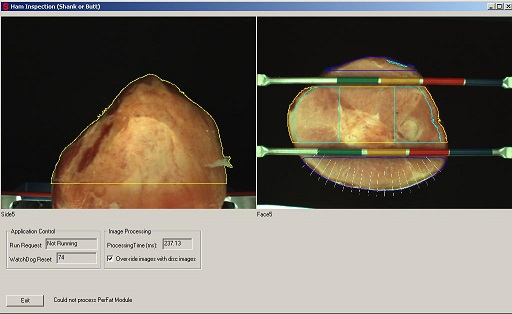
When completed, the script was run to do the inspection. When a bad leaker was detected, it was ejected from the line using Digital IO.
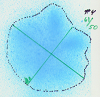
When Valois of America (Norwalk, CT), a manufacturer of drug-delivery devices, wanted to make a system to analyze spray-patters,
they contacted a system integrator on the east coast, who turned to Western for software and expertise.
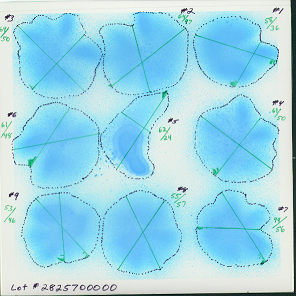
Western helped the system integrator use the HLImage++ API to produce a now FDA approved application called the Valois EZ Spray. See the entire story as printed in Vision Systems Design.
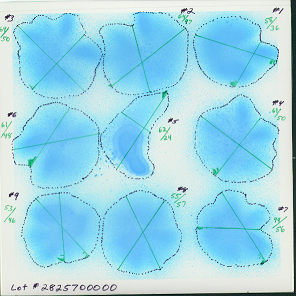
Western helped the system integrator use the HLImage++ API to produce a now FDA approved application called the Valois EZ Spray. See the entire story as printed in Vision Systems Design.
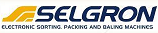
A large manufacturer of sorting machines in Brazil turned to HLImage++ to use in their rice sorting machines.
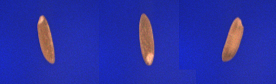
After getting the lighting fine-tuned, they simply wrote a Point & Click Script, tested it, and then exported that script to HLEmbedded.
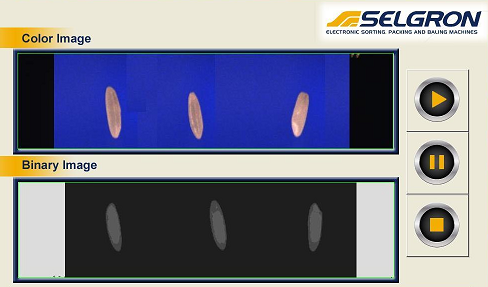
After editing the HLEmbedded INI file to include a custom background, and use custom icons for the stop and exit buttons, they had a custom looking solution based on a script running in HLEmbedded.
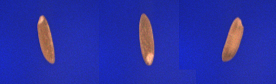
After getting the lighting fine-tuned, they simply wrote a Point & Click Script, tested it, and then exported that script to HLEmbedded.
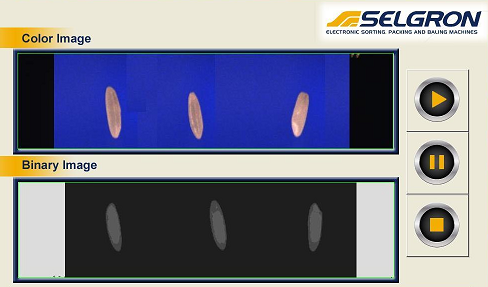
After editing the HLEmbedded INI file to include a custom background, and use custom icons for the stop and exit buttons, they had a custom looking solution based on a script running in HLEmbedded.
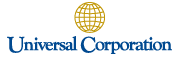
Universal Leaf Tobacco used a mechanical apparatus to quantify tobacco leaves they process.
They wanted a more modern way to measure, inspect, and quantify the tobacco leaves, and they turned to HLImage++.
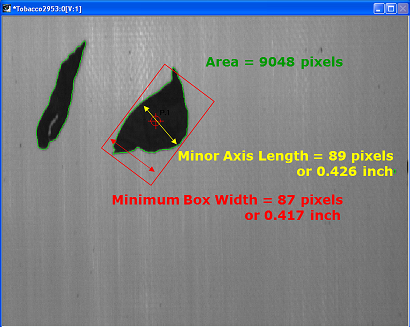
The HLImage++ standard tools were used to report what could be measured, how the measurements were taken, and how the analysis could be displayed.
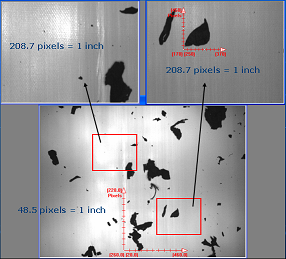
Hundreds of images were taken and analyzed using our HLImage++ product, and Point & Click scripts were written to automate the correct process.
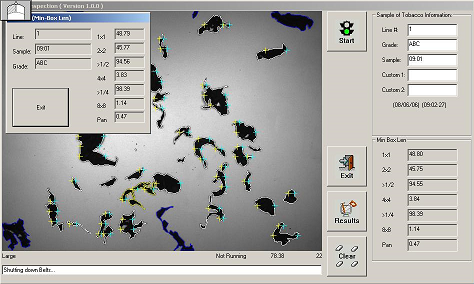
Once the Point & Click Scripts were finalized and tested, they were exported to HLEmbedded to run the conveyer belts the tobacco leaves traveled down, and to gather and report the quantification information needed about the tobacco leaves.
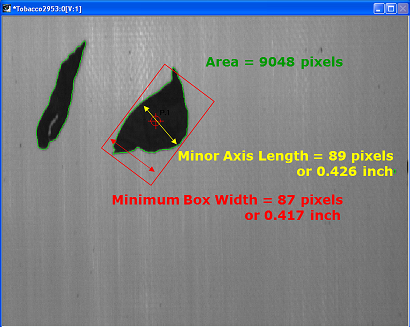
The HLImage++ standard tools were used to report what could be measured, how the measurements were taken, and how the analysis could be displayed.
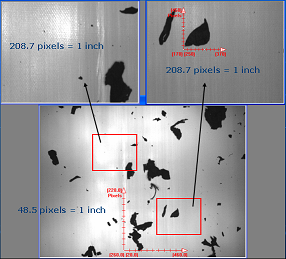
Hundreds of images were taken and analyzed using our HLImage++ product, and Point & Click scripts were written to automate the correct process.
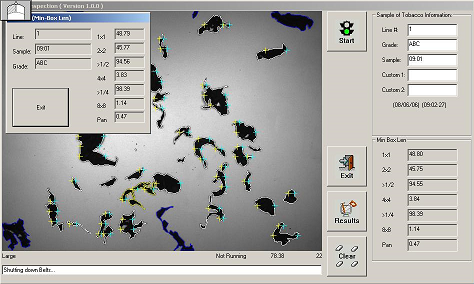
Once the Point & Click Scripts were finalized and tested, they were exported to HLEmbedded to run the conveyer belts the tobacco leaves traveled down, and to gather and report the quantification information needed about the tobacco leaves.

Using an old pallet board does not sound that bad, but it can be.
Turns out, that when pallet boards get old, they start to get delaminated and get their edges broken off.
That leads to them getting hung up in automated factories.
Western was tasked with the interesting problem of finding a way to automatically sort good pallet boards from bad ones. The task was to identify boards with too much delamination or boards with bad edging.
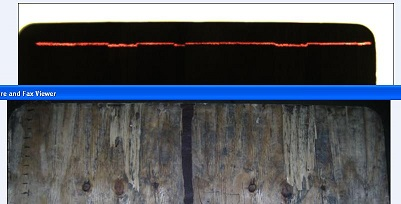
We took a fan laser at an angle and then looked at the resulting line where it hit the board with a camera. Where the board was damaged the line was uneven. We used HLImage++ to create a Point & Click Script that would analyze the red line and determine if the board was damaged, and to what degree.

To inspect the edges and corners, we used the contour tool to make another script that would inspect the outline of the board. This script was able to locate where the corners and edges of a board ‘should be’ even if the corners or edges were broken off. This allowed us to determine if the edges and corners of the board were damaged, and to what degree.
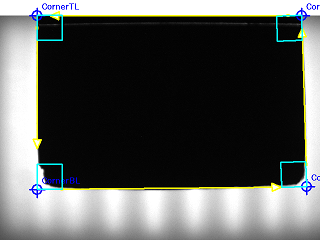
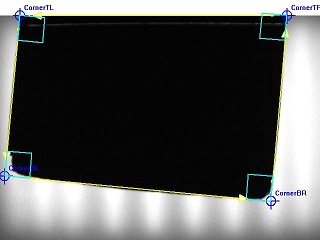
The result was a fully automated process with user defined ejection criteria. The output screen showed the results, as well as an overlaid perfect board outline to the actual aligned board (where the corners and edges of the board should be if the board was not damaged). This allowed an operator to easily make sure the fully automated process was working as expected.
Western was tasked with the interesting problem of finding a way to automatically sort good pallet boards from bad ones. The task was to identify boards with too much delamination or boards with bad edging.
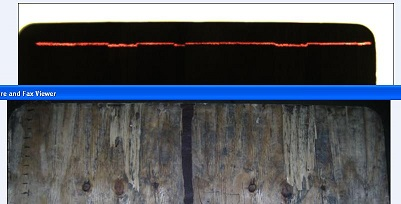
We took a fan laser at an angle and then looked at the resulting line where it hit the board with a camera. Where the board was damaged the line was uneven. We used HLImage++ to create a Point & Click Script that would analyze the red line and determine if the board was damaged, and to what degree.

To inspect the edges and corners, we used the contour tool to make another script that would inspect the outline of the board. This script was able to locate where the corners and edges of a board ‘should be’ even if the corners or edges were broken off. This allowed us to determine if the edges and corners of the board were damaged, and to what degree.
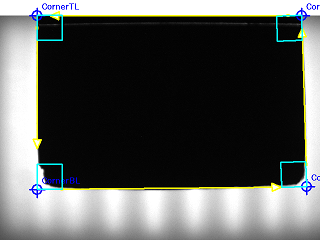
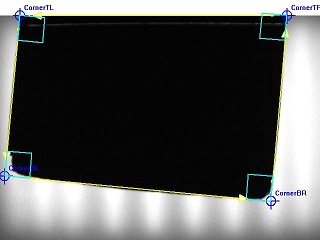
The result was a fully automated process with user defined ejection criteria. The output screen showed the results, as well as an overlaid perfect board outline to the actual aligned board (where the corners and edges of the board should be if the board was not damaged). This allowed an operator to easily make sure the fully automated process was working as expected.

(Seed Counting)
Turns out, seeds sometimes need to be counted when they are sold.
That is why a leading worldwide company in the seed industry wanted a new accurate way to count them.

On 8/19/2008 at 2:05 pm, Western alone created and provided the very first script. This script was then used as the basis of the final script for an optical counter.
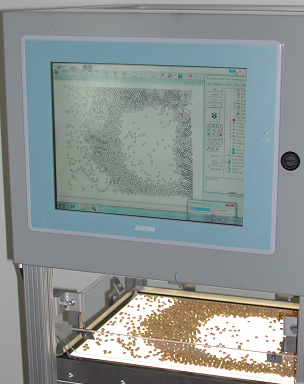
Spanning the term of over five years (and about 400 emails) Western Provided:
This helped lead to the world’s first optical seed counter.
Western worked to fully complete this script, which was then exported to HLEmbedded, and became the world’s first selling patented optical counter for the seed industry.

On 8/19/2008 at 2:05 pm, Western alone created and provided the very first script. This script was then used as the basis of the final script for an optical counter.
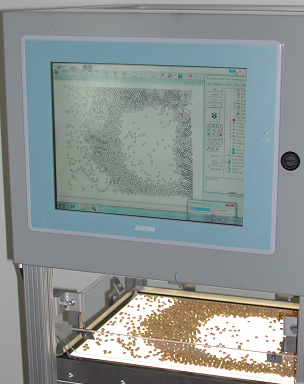
Spanning the term of over five years (and about 400 emails) Western Provided:
|
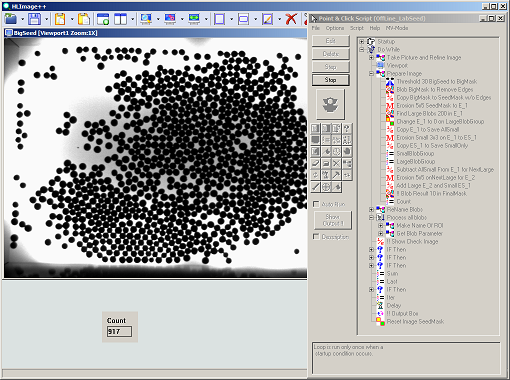
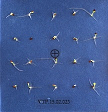
Long before people wanted to count seeds for sale, they wanted to count and track their growth for research.
Before designing software to only count seeds, Western designed software to separate, count, and measure the growth of seeds.
This analysis was done to gather information on temperature, humidity, and other environmental issues that affect the growth of given seeds.
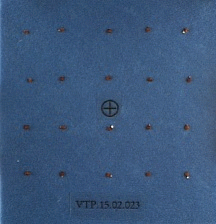
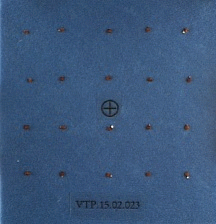
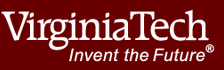
Western is proud to say we have been helping everyone learn about machine vision and image processing by providing HLImage++ in higher education.
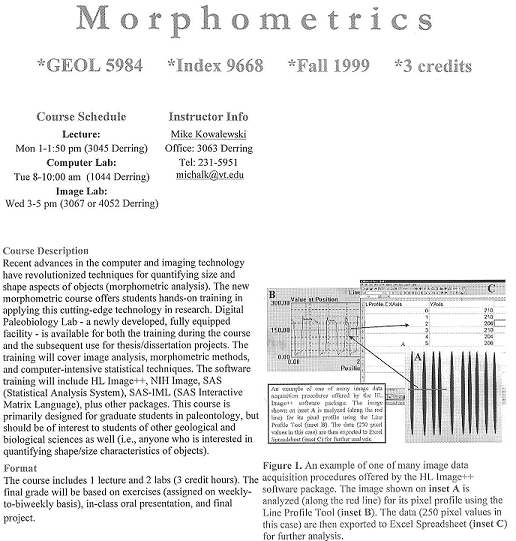
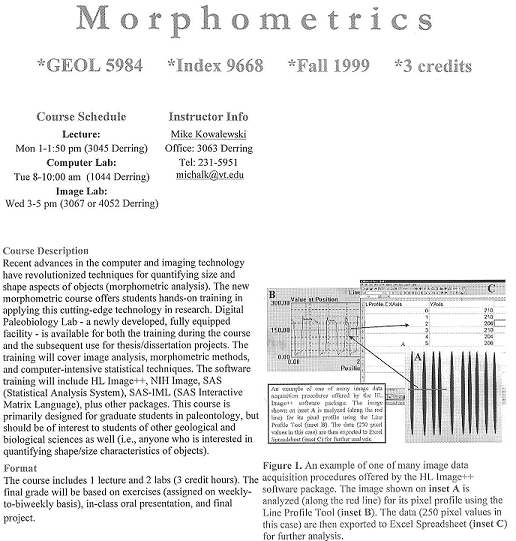
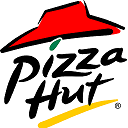
Ever wonder how that yummy Pizza Hut pizza always looks so good and tastes even better, no matter where you are in the world?
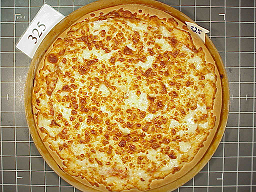
Well, part of the reason is because they analyze many aspects of their pizzas with HLImage++ in their labs.
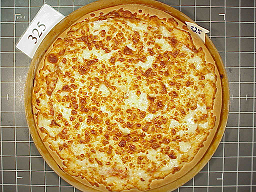
Well, part of the reason is because they analyze many aspects of their pizzas with HLImage++ in their labs.
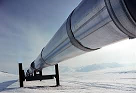
When oil flows through a pipeline it can corrode the pipe itself.
Thus, it is a great idea to find and fix this corrosion before a spill happens.
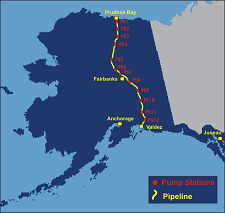
Considering the length of the Alaskan Pipeline, some really smart guys wanted a way to check the pipeline in an automated way. They designed up a machine to crawl along the pipeline, and x-ray the pipe. Western was called in to Prudhue Bay at the northern tip of Alaska. In -70 degrees, we used HLImage++ to show them how to automatically find, size, and classify corrosion pits.
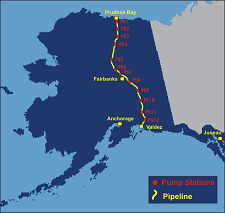
Considering the length of the Alaskan Pipeline, some really smart guys wanted a way to check the pipeline in an automated way. They designed up a machine to crawl along the pipeline, and x-ray the pipe. Western was called in to Prudhue Bay at the northern tip of Alaska. In -70 degrees, we used HLImage++ to show them how to automatically find, size, and classify corrosion pits.
All trademarks, service marks, trade names, trade dress, product names and logos appearing above are the property of their respective owners. If any owner does not wish to have their information listed, please contact us for removal.